レーザーマーキングは、航空業界の発展において重要な技術的利点となっています
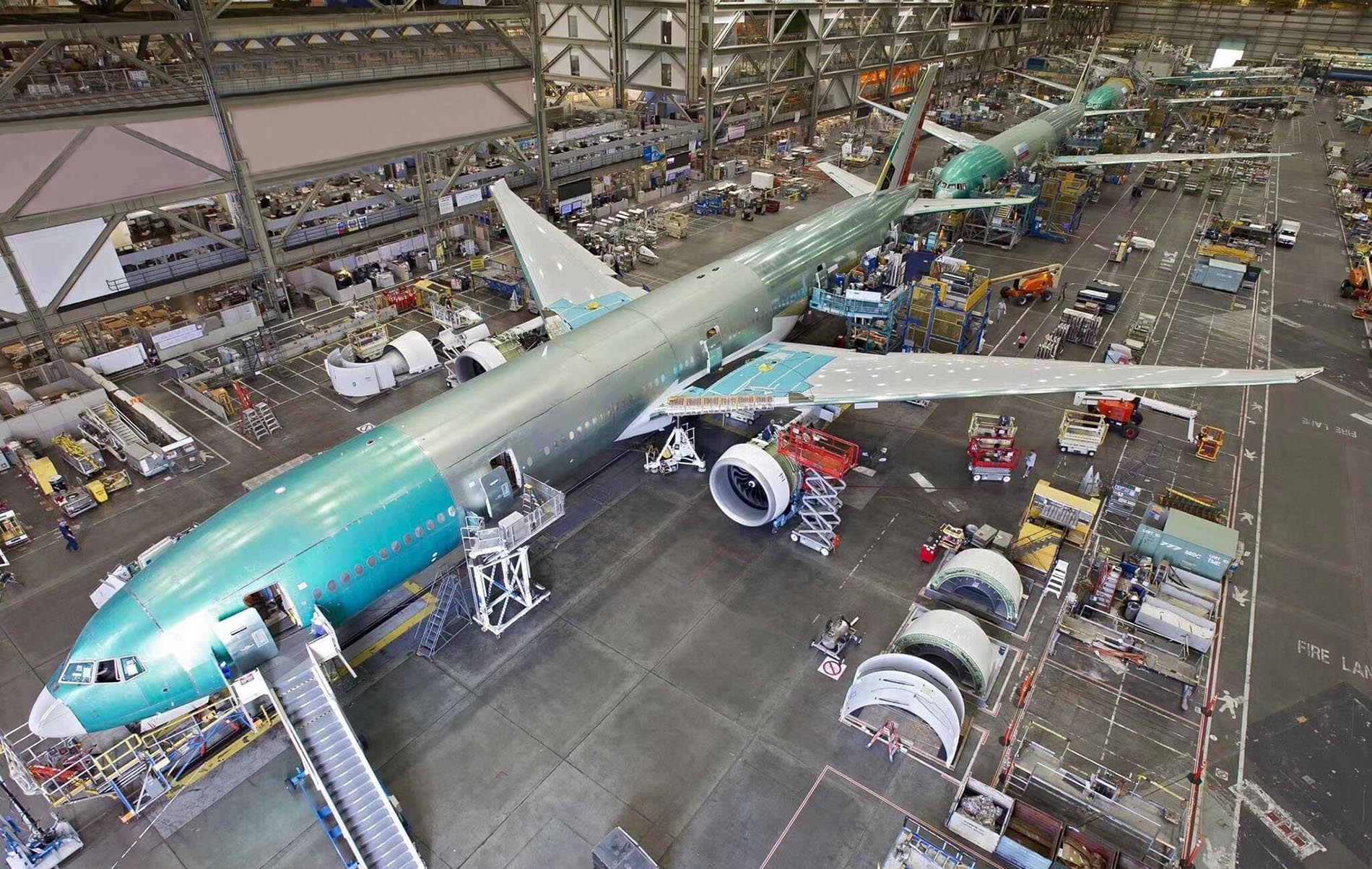
1970年代の高出力レーザーデバイスの誕生以来、レーザー溶接、レーザー切断、レーザー掘削、レーザー表面処理、レーザー合金、レーザークラッディング、レーザー迅速なプロトタイピング、金属部品のレーザー直接形成、および10個以上のアプリケーション。
レーザー加工は、新しい処理技術後の力、火災、電気機械加工であり、高出力レーザーデバイスが70年代から生まれたため、形成や精製など、さまざまな材料処理、完全で思慮深い技術的な問題を解決できます。営業、柔軟性、高品質、省エネと環境保護およびその他の顕著な利点、迅速な自動車、電子機器、航空宇宙、機械、船、国民経済のすべての分野をほぼ含む「処理の一般的な手段」として知られるように広く使用されています。
次の側面に適用します
1.アプリケーションの航空宇宙分野でのレーザー切断技術
航空宇宙産業では、レーザー切断材料は、顎合金、ニッケル合金、クロム合金、アルミニウム合金、ステンレス鋼、チン酸キー、プラスチック、複合材料です。
航空宇宙機器の製造では、特別な金属材料の使用、高強度、高硬度、高温耐性、通常の切断方法の使用のシェルは、材料処理を完了するのが困難です。レーザー切断は処理の効果的な手段です。
通常、レーザー切断が使用されます連続出力レーザー、ただし、高周波二酸化炭素パルスレーザーも有用です。レーザー切断深さと幅の比率は高く、非金属の場合、深さと幅の比率は100以上に達する可能性があり、金属は約20個に達することができます。
レーザー切断速度が高い、顎合金シートは機械的な方法について30倍です。鋼板を切断することは機械的方法の20倍です。
レーザー切断品質は良いです。酸素アセチレンおよびプラズマ切断方法と比較して、炭素鋼の切削は最高の品質を持っています。レーザー切断の熱罹患ゾーンは、酸素アセチレンのみです。
2.航空宇宙分野におけるレーザー溶接技術の適用
航空宇宙産業では、レーザー溶接を真空で行う必要がないため、多くの部品に電子ビームが溶接されています。レーザー溶接は電子ビーム溶接を交換するために使用されています。
長い間、航空機の構造部品間の接続は後方リベット技術の使用でした。主な理由は、航空機構造で使用されるアルミニウム合金が熱処理補強材合金(すなわち、高強度アルミニウム合金)であるため、融合溶接、熱処理強化効果が失われ、顆粒層が回避できないことです。
レーザー溶接技術の採用は、そのような問題を克服し、航空機の胴体の製造プロセスを大幅に簡素化し、胴体の重量を18%、コストを21.4%〜24.3%削減します。レーザー溶接技術は、航空機製造業界の技術革命です。
3.航空宇宙分野におけるレーザー掘削技術のアプリケーション
レーザー掘削技術は、航空宇宙産業で使用され、機器の宝石ベアリング、空冷タービンブレード、ノズル、燃焼器に穴を開けます。現在、レーザー掘削は、穴の表面に微視的な亀裂があるため、固定エンジン部品の冷却穴に限定されています。
レーザービーム、電子ビーム、エレクトロ化学、EDM掘削、機械的掘削、パンチングの実験的研究は、包括的な分析によって結論付けられています。レーザー掘削には、良好な効果、強力な汎用性、高効率、低コストの利点があります。
4.航空宇宙分野におけるレーザー表面技術のアプリケーション
レーザークラッディングは、重要な材料表面修正技術です。航空では、エアロエンジンのスペアパーツの価格が高いため、多くの場合、部品を修理するのが費用対効果が高くなります。
ただし、修理された部品の品質は安全要件を満たす必要があります。たとえば、航空機のプロペラブレードの表面に損傷が現れる場合、いくつかの表面処理技術で修復する必要があります。
プロペラブレードに必要な高強度と疲労抵抗に加えて、表面修復後の耐食性も考慮する必要があります。レーザークラッディングテクノロジーを使用して、エンジンブレードの3D表面を修復できます。
5.航空宇宙分野におけるレーザー形成技術のアプリケーション
航空におけるレーザー形成の製造技術の適用は、航空のためのチタン合金構造部品の直接製造と航空機のエンジン部品の迅速な修復に直接反映されています。
レーザー形成製造技術は、航空宇宙防衛兵器と機器の大型チタン合金構造部分のコア新しい製造技術の1つになりました。従来の製造方法には、高コスト、鍛造カビ、大量の機械的処理、および低材料利用率の長い準備時間の欠点があります。